The blown film machine adopts A and B double main engines. After the machine head, the two materials of the two mainframes are formed into a three-layer film. The ABA structure has a strong blown film, hard hand feeling, good brightness, high output and strong puncture resistance. And the middle layer can be added with cheap materials to reduce costs.
The 3 layers extruder machine only needs two main machines, one squeezes the inner and outer layers (layer A), and one squeezes the middle sandwich layer (layer B) using recycled materials or other cheap materials, even adding 50% calcium carbonate.
Its strength, weldability, and printability are unaffected, and the middle layer is cooled faster by the addition of calcium carbonate or low pressure polyethylene. Because the die of the three-layer co-extrusion blown film machine has three channels to reduce the pressure loss, the thickness of the film is more uniform, and the power consumption is more economical.
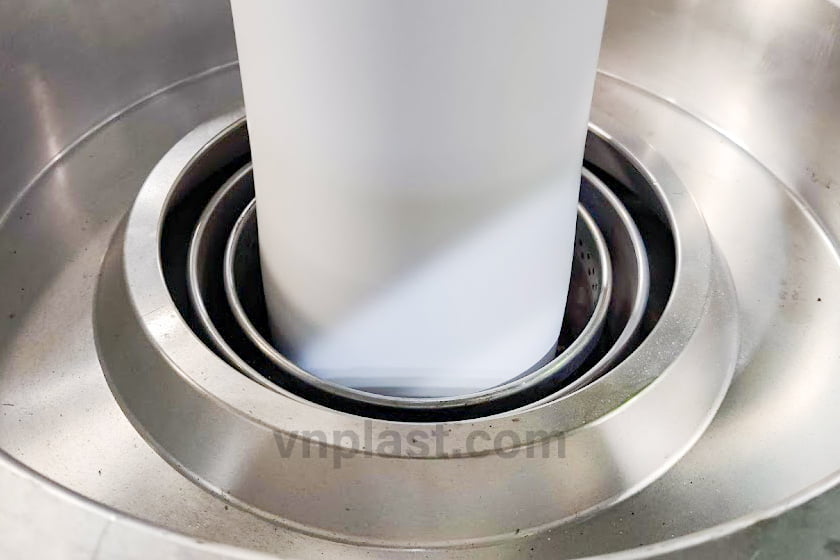
Moreover, there are only three main channels and three channels, and each ton of film is installed with the inverter in the blower. It can save about 200 kWh than a single blown film. This is unprecedented in the production of single-machine single-die or three-story old-fashioned three-host. Undoubtedly bring the gospel to the sustainable development of the blown film industry.
ABA blowing machine is used for: blowing high and low pressure polyethylene films (LDPE, HDPE), products are widely used in packaging of composite films, packaging bags, agricultural covering films, textiles, clothing bags, etc. The main motor adopts frequency conversion speed regulation, which increases The stability of the main machine can save electricity, and the traction frame adopts a lifting type, which can achieve the best film cooling effect.